Human-Centered Shears
Scissors are a young man's game. Innovation calls for ergonomic improvements.
OBJECTIVE:
Design an alternative to the current cutting techniques that cause hand pain
TOURING A FACTORY.
I visited Casco Manufacturing Solutions in Cincinnati, OH to document their operations, aiming to understand their use of human labor and to identify opportunities for improving both worker comfort and productivity.
UNCOVERING THE ISSUE
Here, I discovered that most of CASCO’s factory workers were seamstresses aged 50 or older. They had been tirelessly cutting fabric using heavy metal tailor shears, which had resulted in pain and arthritis in their finger joints. After hearing their struggles, I knew I had to take action.
This became my area of opportunity: How can I make their job more comfortable?
ALIGNING WITH A BRAND.
In my pursuit of elevating the aesthetic appeal of my shear design, I discovered RELIABLE, a company firmly dedicated to excellence in the fabric and textile industry. Their high-quality and affordable tools seamlessly aligned with my overall vision and values, ensuring accessibility to a broad audience
By leveraging RELIABLE's brand to inspire my design, I gained confidence that my product would become a comfortable, affordable, and user-friendly tool, accessible to a diverse range of users.
HOUSEHOLD
INDUSTRIAL
COMMERCIAL
STUDYING THE PROCESS.
To formulate an effective solution for the workers, I recognized the need to closely examine their daily work processes, with a particular focus on their use of shears step-by-step.
BRAINSTORM.
IDEATION OBJECTIVE:
Develop a pair of electronic shears that seamlessly blend ergonomic comfort with precision cutting capabilities while incorporating a rechargeable power source.
ERGONOMIC STUDIES
what feels natural + comfortable to the user?
EXPLORATION
what if shears had a trigger mechanism instead of a pinch grip?
PROTOTYPING
Insulation foam underwent sanding to shape prototype forms, enabling ergonomic, handle, and trigger testing.
INNER COMPONENTS STUDY.
In my research, I explored the workings of other electronic power tools and used that knowledge to methodically plan the integration of motors, batteries, and components into my design, significantly shaping its form and layout.
FINAL PROTOTYPE.
For the final physical model, I used a CNC machine to precisely shape the tool's body. Smaller intricate details, beyond the CNC's capabilities, were resin-printed and assembled to create an ultra-realistic prototype for ergonomic testing.
8.5” TALL
RESIN PARTS
FINAL RENDERS.
The final design revolutionizes the cutting experience by replacing the traditional arm and pinch grip method with a pull-trigger mechanism and smooth surface glide.
This approach not only enhances precision and comfort but also minimizes wrist and hand strain, offering a more user-friendly and accurate cutting solution.
COMFORTABLE
PRECISION
RECHARGEABLE
CUTTING-EDGE
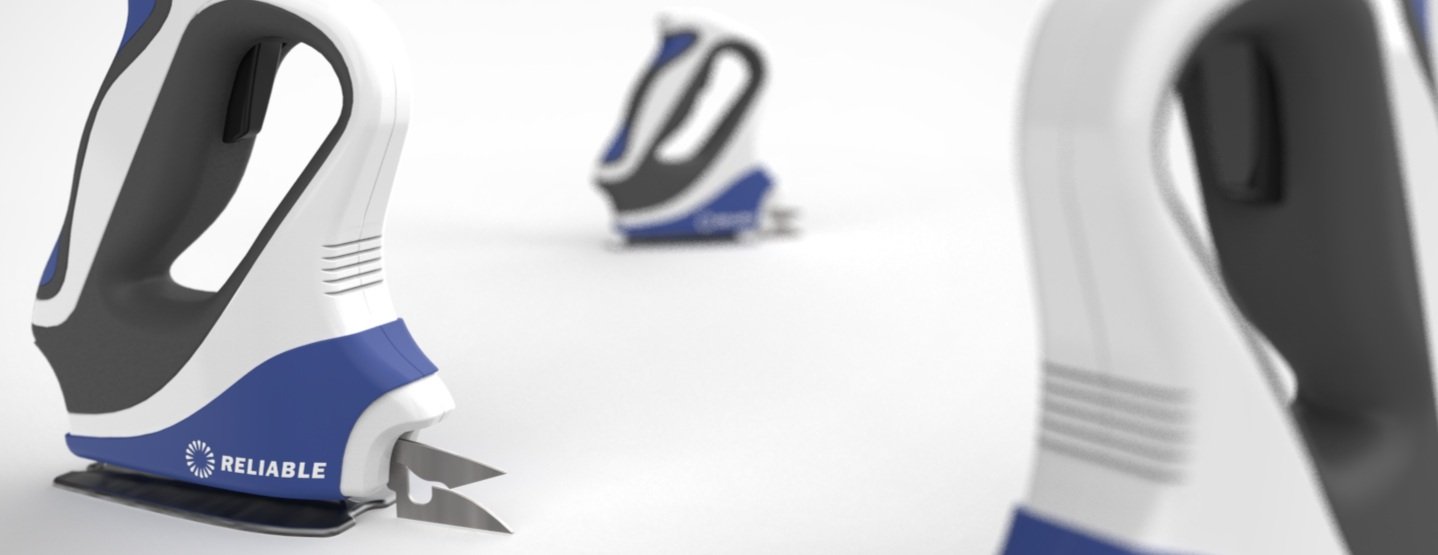
SHEAR INNOVATION.
RETURN HOME
RESTART PAGE
OTHER PROJECTS